How we produce - EPT arm rests
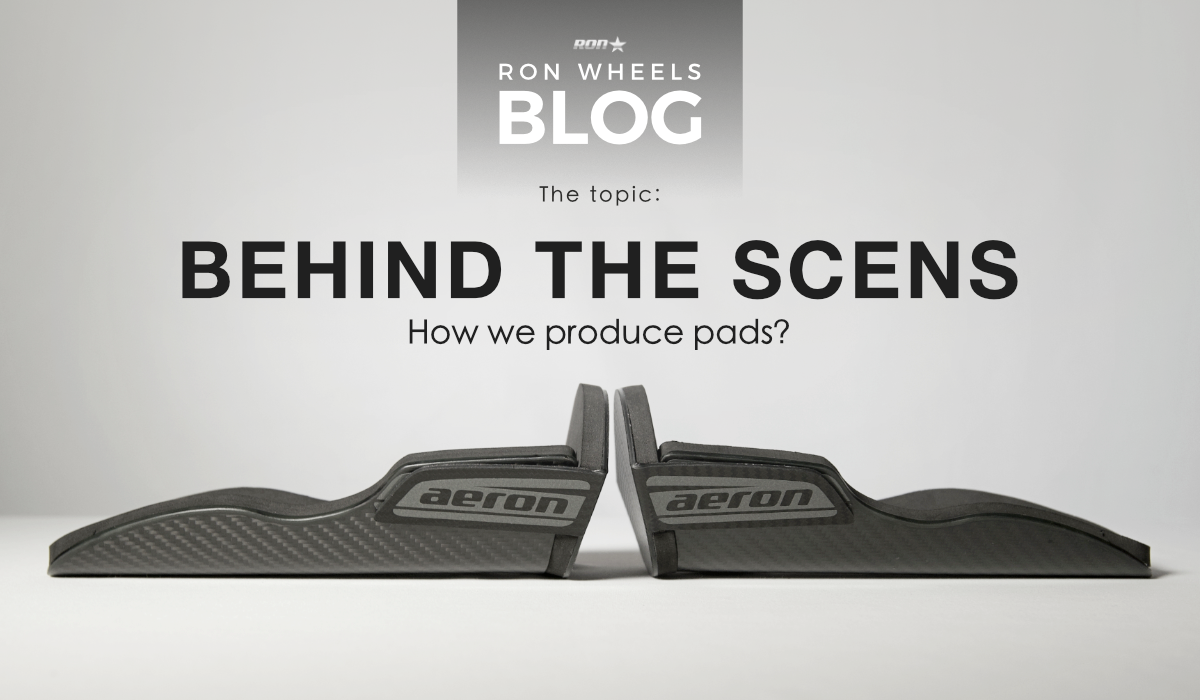
Welcome to our blog, where today we invite you on a journey into the world of EPT arm rest production! In this article, we'll delve into the intricacies of creating these crucial components of ergonomic equipment. We'll explore the stages through which raw carbon material undergoes to transform into exceptional supports for our arms. Exciting discoveries await us regarding technology, precision, and passion that shape each production step. Are you ready for an insightful look behind the scenes? Get ready for a journey through the process of creating EPT arm rests!
PRODUCTION STAGES:
1.Thawing and cutting carbon prepreg: In this phase, raw carbon material is thawed to achieve the appropriate flexibility and ease of processing. (To maintain freshness, the material must be stored at a very low temperature.) Then it is precisely cut into suitable templates that will be used for further production
2. Bonding various carbon fiber templates: Many templates made of different types of carbon fibers are carefully arranged and bonded into a multi-layered plate. This process aims to create a structure with optimal strength and rigidity, which is crucial for the final product.
3. Forming in steel molds and packing into vacuum bags: Cut carbon shapes are placed into steel molds, which give them their final shape. Then the molds are carefully packed into special vacuum bags to ensure a uniform and precise hardening process.
4. Curing in the oven: Bags with molds are placed into an oven where they are subjected to controlled high temperature and pressure. This manufacturing process ensures that carbon achieves its ultimate strength and durability, which is crucial for producing high-quality arm rests.
5. Post-mold processing: When the arm rest is removed from the mold, it undergoes post-mold processing, which includes precise edge grinding to achieve a smooth finish and CNC machining of mounting holes for dimensional accuracy and consistency.
6. Coating: After completing the processing, the product undergoes a coating process, which not only adds aesthetics but also protects the surface from mechanical damage and atmospheric conditions.
7. Final touch and shipping: In the final stage, foam is applied to the arm rest to provide comfort, along with the AERON logo. After completing these processes, the finished product is packaged and shipped to customers who expect improved performance, comfort, and speed.
Comments
No comment at this time!
Leave your comment